Studio CMMS.net jest systemem eksperckim, którego zadaniem jest pomoc w dostosowaniu zakładu do wymogów dyrektywy maszynowej jak i w żmudnych codziennych działaniach osób dzięki którym produkcja idzie oczekiwanym rytmem.
Studio CMMS.net – System ekspercki dla efektywnego zarządzania utrzymaniem ruchu
Wprowadzenie do Studio CMMS.net
Studio CMMS.net to zaawansowany system ekspercki, który został stworzony w celu wsparcia zakładów przemysłowych w dostosowaniu się do wymogów dyrektywy maszynowej oraz w codziennych działaniach związanych z utrzymaniem ruchu maszyn. Dzięki Studio CMMS.net możliwe jest skuteczne zarządzanie procesami konserwacyjnymi i naprawczymi, co przekłada się na płynność produkcji i optymalne wykorzystanie zasobów.
Zgodność z dyrektywą maszynową
Studio CMMS.net jest specjalnie zaprojektowane, aby pomóc zakładom przemysłowym w spełnieniu wymogów dyrektywy maszynowej. System oferuje narzędzia i funkcje umożliwiające dokumentowanie i monitorowanie zgodności maszyn oraz prowadzenie odpowiedniej dokumentacji technicznej. Dzięki temu użytkownicy mogą mieć pewność, że ich zakład spełnia wszelkie normy i standardy bezpieczeństwa.
Zarządzanie utrzymaniem ruchu
Głównym celem Studio CMMS.net jest umożliwienie efektywnego zarządzania utrzymaniem ruchu maszyn. System oferuje szereg narzędzi, takich jak harmonogramy, planowanie zadań, monitorowanie wydajności, rejestrowanie awarii i napraw, zarządzanie zasobami, a także generowanie raportów i analiz danych. Dzięki temu użytkownicy mogą skutecznie organizować i monitorować wszystkie działania związane z utrzymaniem ruchu, co przekłada się na minimalizację przestojów i zwiększenie wydajności produkcji.
Korzyści wynikające z Studio CMMS.net
Studio CMMS.net oferuje wiele korzyści dla zakładów przemysłowych. Przede wszystkim, umożliwia optymalne wykorzystanie zasobów, poprzez skuteczne planowanie i realizację zadań konserwacyjnych. Dodatkowo, system pozwala na szybką identyfikację i naprawę awarii, co minimalizuje przestoje i koszty związane z utrzymaniem maszyn.
Kolejną korzyścią jest możliwość generowania szczegółowych raportów i analiz, które dostarczają cennych informacji o wydajności maszyn, zużyciu części, kosztach utrzymania oraz innych kluczowych wskaźnikach. Dzięki temu, użytkownicy mogą podejmować świadome decyzje dotyczące dalszych działań i optymalizować procesy utrzymania ruchu.
Podsumowując, Studio CMMS.net jest zaawansowanym systemem eksperckim, który umożliwia efektywne zarządzanie utrzymaniem ruchu maszyn. Dzięki zgodności z dyrektywą maszynową oraz bogatym zestawem narzędzi i funkcji, użytkownicy mogą skutecznie planować, monitorować i optymalizować procesy konserwacyjne, co przekłada się na płynność produkcji i zwiększenie efektywności działania zakładu przemysłowego.
Studio CMMS.net
Trudno sobie wyobrazić nowoczesne przedsiębiorstwo produkcyjne lub zakład przemysłowy bez dobrze zorganizowanego działu zajmującego się utrzymaniem ruchu. Studio CMMS.net to zaawansowane oprogramowanie do zarządzania konserwacją i naprawami maszyn oraz urządzeń w firmach produkcyjnych i logistycznych.
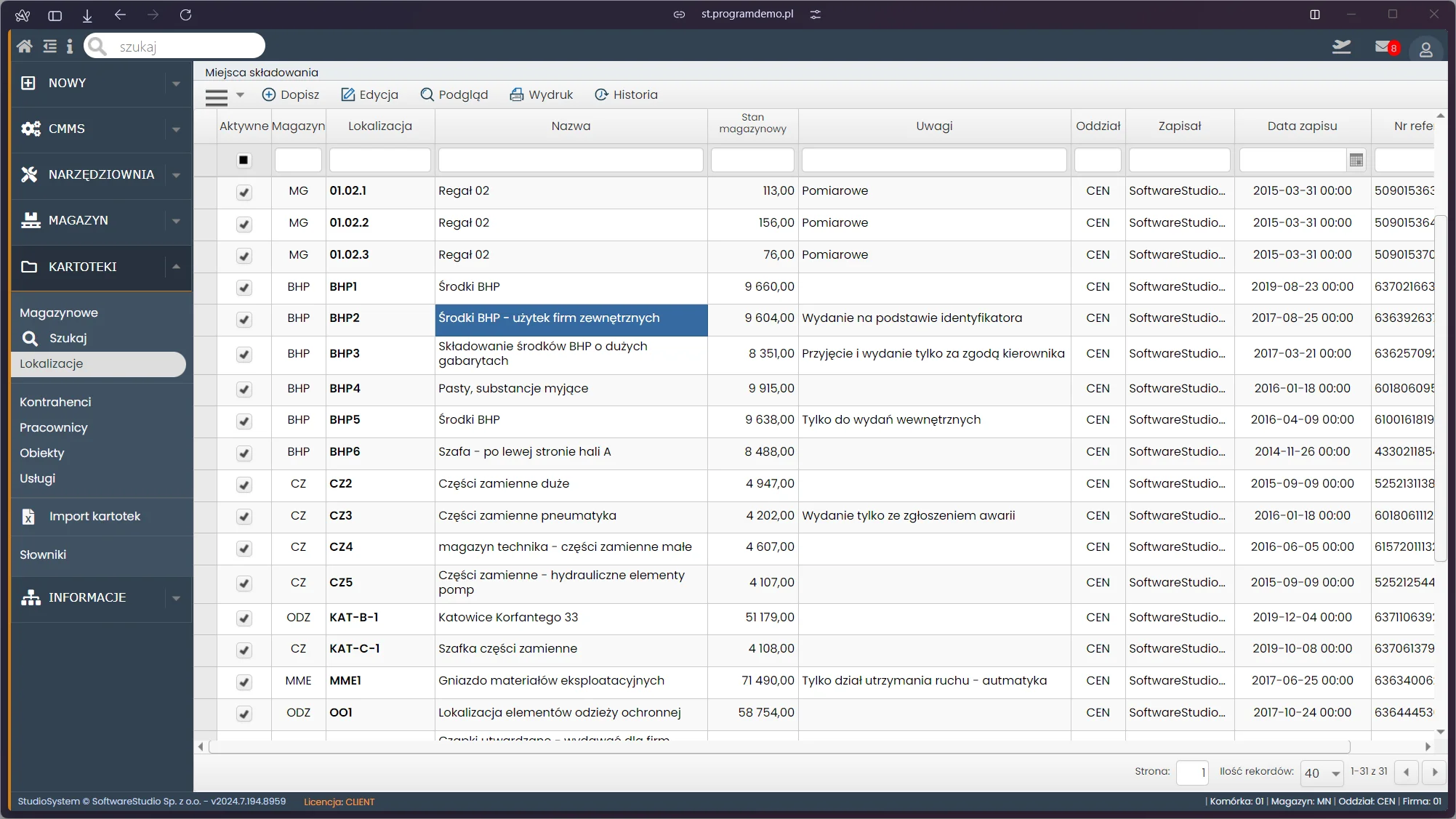
Monitorowanie stanu technicznego
System umożliwia monitorowanie stanu technicznego maszyn i urządzeń. Dzięki temu kierownicy zakładów mogą szybko reagować na wszelkie nieprawidłowości, co minimalizuje ryzyko awarii. Program do zarządzania narzędziownią oferowany przez Studio TCS.net pozwala na bieżące śledzenie i analizowanie danych technicznych, co znacząco zwiększa niezawodność maszyn.
Planowanie przeglądów
Studio CMMS.net umożliwia planowanie przeglądów technicznych, co pozwala na regularne sprawdzanie stanu maszyn i zapobieganie awariom. Programy dla narzędziowni umożliwiają ustalanie harmonogramów przeglądów oraz przypominają o nadchodzących terminach. To zapewnia ciągłość pracy i minimalizuje ryzyko przestojów.
Zarządzanie awariami
Oprogramowanie umożliwia także zarządzanie awariami. W przypadku wystąpienia usterki, system generuje zlecenie pracy, które jest śledzone aż do zakończenia naprawy. Dzięki temu, gospodarka narzędziowa jest bardziej efektywna, a naprawy przeprowadzane są szybko i sprawnie. System do zarządzania narzędziami, oferowany przez SoftwareStudio, umożliwia pełną kontrolę nad procesem naprawczym.
Współpraca Studio TCS.net i narzędziowni
Program Studio TCS.net i narzędziownia współpracują ze sobą, tworząc kompleksowe rozwiązanie do zarządzania utrzymaniem ruchu. Program do ewidencji narzędzi pozwala na dokładne śledzenie stanu i lokalizacji narzędzi, co wspiera planowanie i realizację przeglądów oraz napraw. Dzięki temu możliwe jest zwiększenie efektywności pracy oraz redukcja kosztów związanych z przestojami i awariami.
Podsumowanie
Podsumowując, Studio CMMS.net to kluczowe narzędzie dla nowoczesnych przedsiębiorstw produkcyjnych i zakładów przemysłowych. Umożliwia monitorowanie stanu technicznego, planowanie przeglądów oraz zarządzanie awariami, co minimalizuje ryzyko przestojów i zwiększa efektywność pracy. Program Studio TCS.net i narzędziownia współpracują ze sobą, tworząc skuteczne rozwiązanie do zarządzania utrzymaniem ruchu i ewidencją narzędzi.
Podstawowe zadania oprogramowania Studio CMMS.net
Zadanie | Opis |
---|---|
Ewidencja maszyn i urządzeń | Program umożliwia dokładną ewidencję maszyn i urządzeń, co pozwala na łatwe zarządzanie nimi oraz dostęp do niezbędnych informacji. |
Osprzęt i narzędzia | Rejestracja i monitorowanie stanu osprzętu i narzędzi, co ułatwia zarządzanie zasobami. |
Magazyn części zamiennych | Kontrola i zarządzanie magazynem części zamiennych, co pozwala na szybkie reagowanie na potrzeby napraw. |
Awarie | Rejestracja i monitorowanie awarii, co umożliwia szybkie reagowanie oraz analizę przyczyn. |
Przeglądy | Planowanie i realizacja przeglądów technicznych maszyn i urządzeń, co zapobiega awariom i przedłuża ich żywotność. |
Historia zdarzeń | Rejestrowanie historii zdarzeń związanych z maszynami i urządzeniami, co pozwala na analizę i optymalizację procesów. |
Harmonogramy | Tworzenie harmonogramów przeglądów, konserwacji i napraw, co ułatwia planowanie i realizację działań utrzymaniowych. |
Ewidencja pracowników | Rejestracja i monitorowanie pracowników, ich obowiązków oraz uprawnień, co ułatwia zarządzanie zespołem. |
Obliczanie kosztów oraz ilości roboczogodzin | Program umożliwia obliczanie kosztów oraz ilości roboczogodzin związanych z naprawami i przeglądami, co pomaga w optymalizacji budżetu. |
Dokumentacja, zasoby w formie załączników | Możliwość dodawania i przechowywania dokumentacji oraz zasobów w formie załączników, co ułatwia dostęp do potrzebnych informacji. |
Statystyki i wskaźniki | Generowanie statystyk oraz wskaźników takich jak średni czas awarii, średni czas między awariami oraz wskaźnik wykorzystania wyposażenia, co umożliwia analizę i optymalizację działań. |
Procedura RCM w utrzymaniu ruchu: Optymalizacja działań konserwacyjnych
Wprowadzenie do procedury RCM
Reliability Centered Maintenance (RCM) to procedura, która ma na celu określenie niezbędnych działań utrzymania w celu zapewnienia sprawności eksploatacyjnej urządzenia lub maszyny. Procedura RCM uwzględnia warunki użytkowania, znaczenie dla procesu produkcyjnego oraz jakość wyrobu. Jest to podejście, które pozwala na optymalizację działań konserwacyjnych, minimalizację awarii i przestojów oraz zwiększenie efektywności działania zakładu przemysłowego.
Kroki procedury RCM
Procedura RCM składa się z kilku kroków, które umożliwiają kompleksową analizę urządzeń i maszyn. Poniżej przedstawiamy główne etapy tej procedury:
Identyfikacja funkcji urządzenia
W pierwszym kroku identyfikuje się kluczowe funkcje, jakie urządzenie spełnia w procesie produkcyjnym. Określa się również oczekiwane wyniki tych funkcji, co pozwala na lepsze zrozumienie roli urządzenia w całym procesie.
Analiza awarii
Następnie przeprowadza się analizę możliwych awarii i ich skutków. Szczególną uwagę zwraca się na awarie, które mogą mieć istotny wpływ na proces produkcyjny, jakość wyrobu lub bezpieczeństwo. Ta analiza pomaga w identyfikacji potencjalnych zagrożeń i obszarów wymagających szczególnej uwagi.
Wybór strategii utrzymania
Na podstawie analizy awarii, decyduje się, jakie strategie utrzymania będą stosowane dla poszczególnych komponentów urządzenia. Może to obejmować konserwację zapobiegawczą, diagnostykę stanu technicznego, naprawy, modernizacje itp. Wybór odpowiedniej strategii jest kluczowy dla efektywnego zarządzania urządzeniami.
Określenie działań konserwacyjnych
Następnie określa się konkretne działania konserwacyjne, które należy wykonać w ramach wybranej strategii utrzymania. Wskazuje się, jak często i w jaki sposób te działania powinny być przeprowadzane. To zapewnia, że urządzenia będą działały zgodnie z oczekiwaniami i minimalizuje ryzyko awarii.
Implementacja i monitorowanie
W kolejnym etapie procedury RCM, implementuje się określone działania konserwacyjne i monitoruje ich skuteczność. Na podstawie monitoringu można dostosowywać strategie i działania w celu optymalizacji utrzymania ruchu. Regularne monitorowanie pozwala na bieżąco kontrolować stan techniczny urządzeń i wprowadzać potrzebne korekty.
Korzyści płynące z procedury RCM
Zastosowanie procedury RCM w utrzymaniu ruchu maszyn i urządzeń przemysłowych przynosi szereg korzyści. Oto niektóre z głównych korzyści wynikających z implementacji procedury RCM:
Zwiększenie dostępności i niezawodności maszyn
Poprzez skoncentrowanie się na kluczowych funkcjach i właściwym doborze działań konserwacyjnych, można znacząco zwiększyć dostępność i niezawodność maszyn. Systematyczne działania prewencyjne i dokładna kontrola stanu technicznego urządzeń zapewniają ich ciągłą i efektywną pracę.
Minimalizacja ryzyka awarii i przestojów
Analiza awarii oraz wprowadzenie odpowiednich strategii utrzymania pozwala na minimalizację ryzyka awarii i przestojów produkcyjnych. To przekłada się na ciągłość procesu produkcyjnego i zapewnia, że maszyny są zawsze gotowe do pracy, co zwiększa efektywność operacyjną zakładu.
Optymalizacja kosztów utrzymania
Dzięki precyzyjnemu określeniu działań konserwacyjnych i ich harmonogramu, możliwa jest optymalizacja kosztów utrzymania. Efektywne wykorzystanie zasobów i unikanie niepotrzebnych napraw przekłada się na oszczędności finansowe, jednocześnie zapewniając, że urządzenia są w odpowiednim stanie technicznym.
Zwiększenie bezpieczeństwa
Procedura RCM uwzględnia także aspekt bezpieczeństwa, pozwalając na identyfikację i eliminację potencjalnych zagrożeń dla pracowników i środowiska. Regularne przeglądy i konserwacje minimalizują ryzyko awarii, które mogłyby prowadzić do niebezpiecznych sytuacji, zapewniając bezpieczne warunki pracy.
Podsumowując, procedura RCM stanowi skuteczne narzędzie w utrzymaniu ruchu maszyn i urządzeń przemysłowych. Pozwala na efektywne planowanie i realizację działań konserwacyjnych, minimalizację awarii i przestojów, oraz optymalizację kosztów utrzymania. Dzięki temu, zakład przemysłowy może osiągnąć wysoką dostępność i niezawodność maszyn, co przekłada się na efektywność produkcji i satysfakcję klientów.
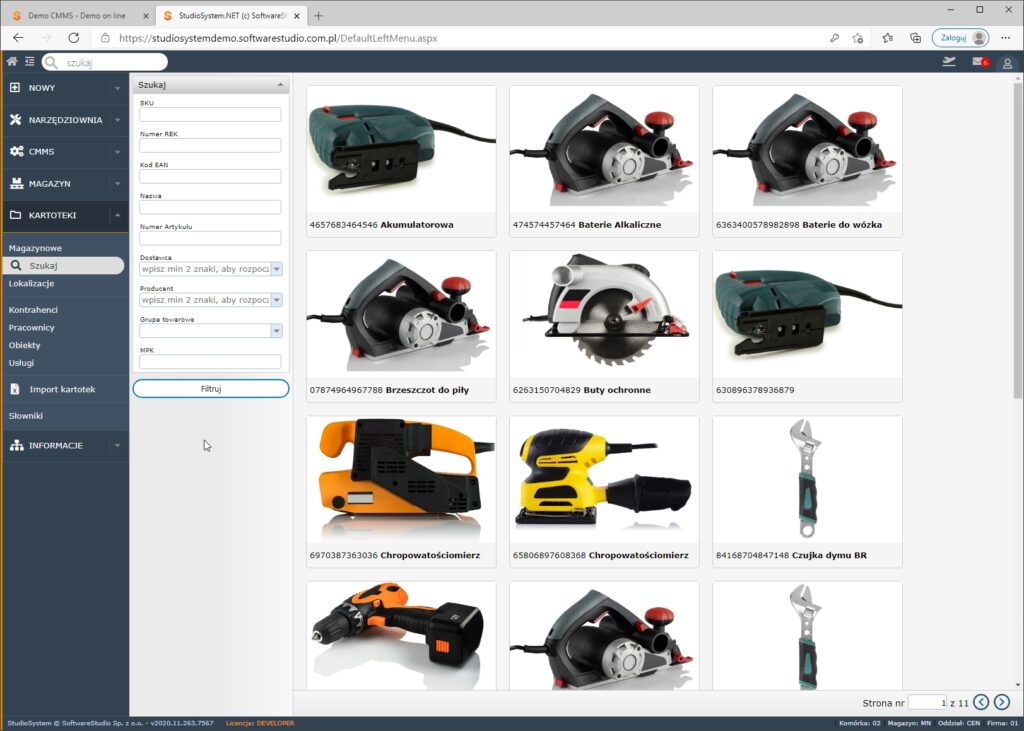
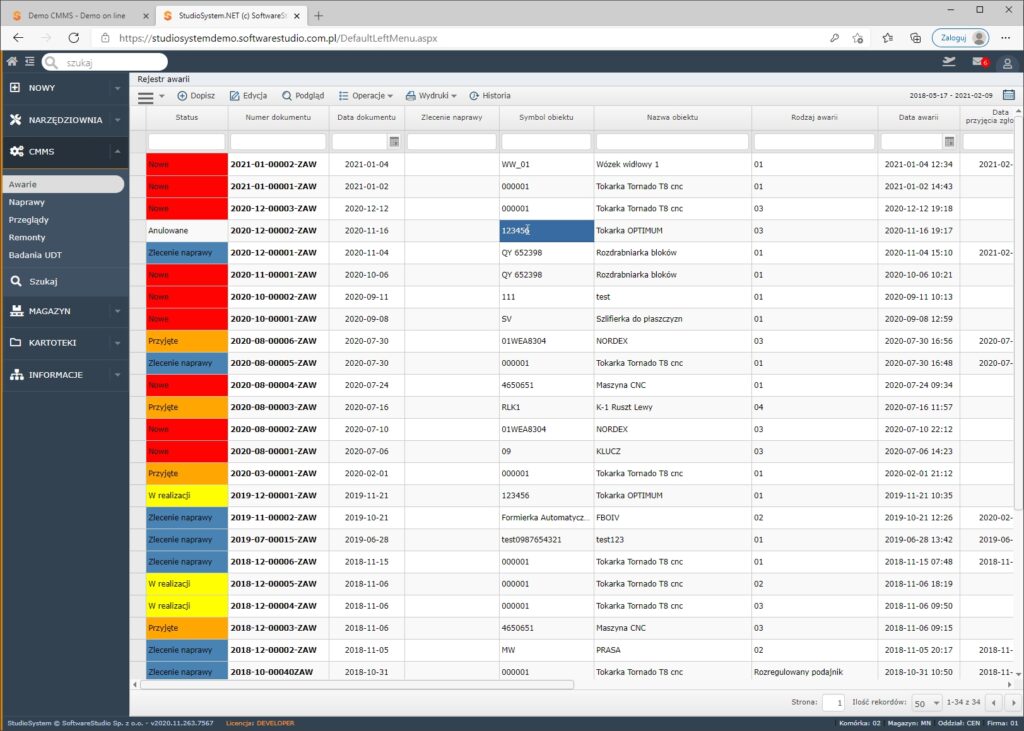
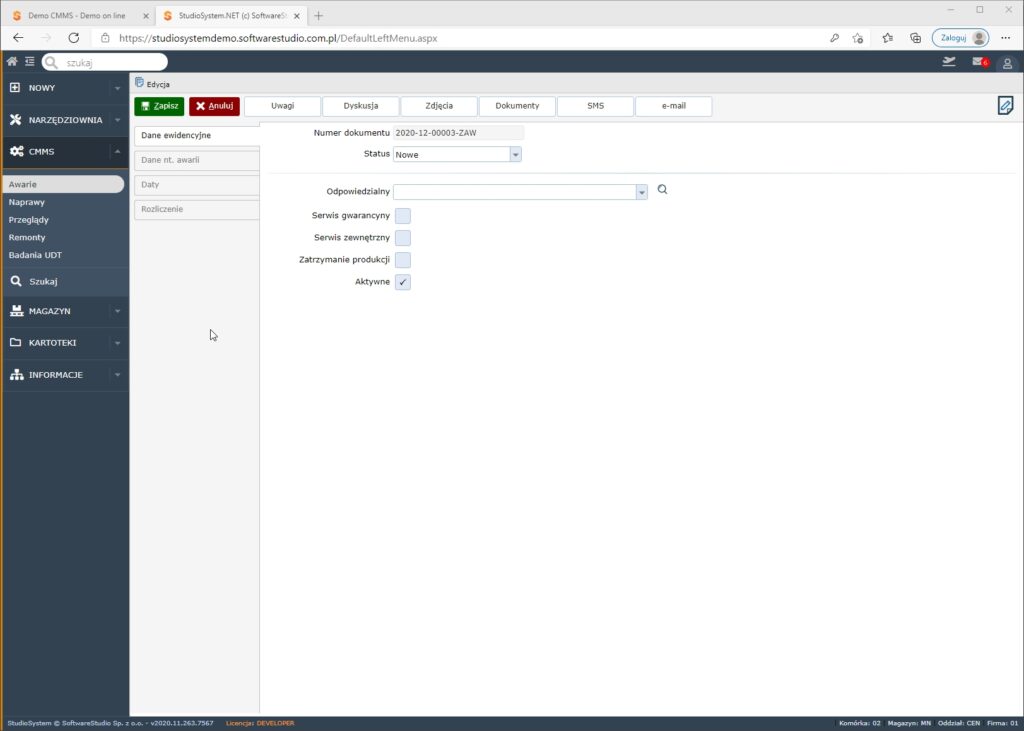
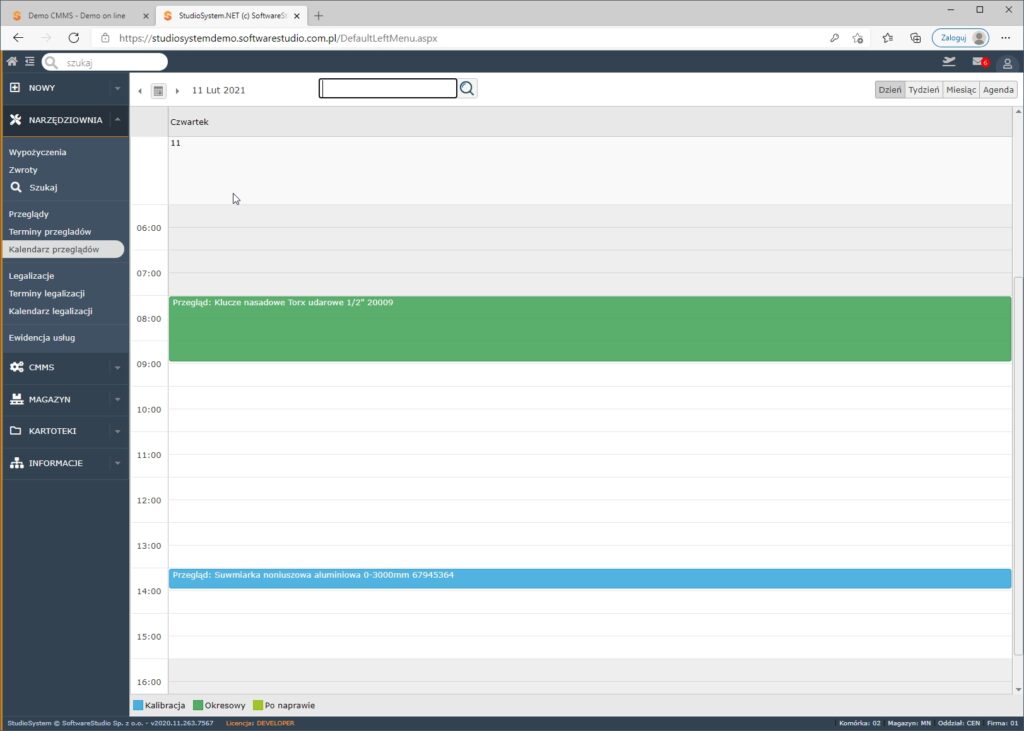
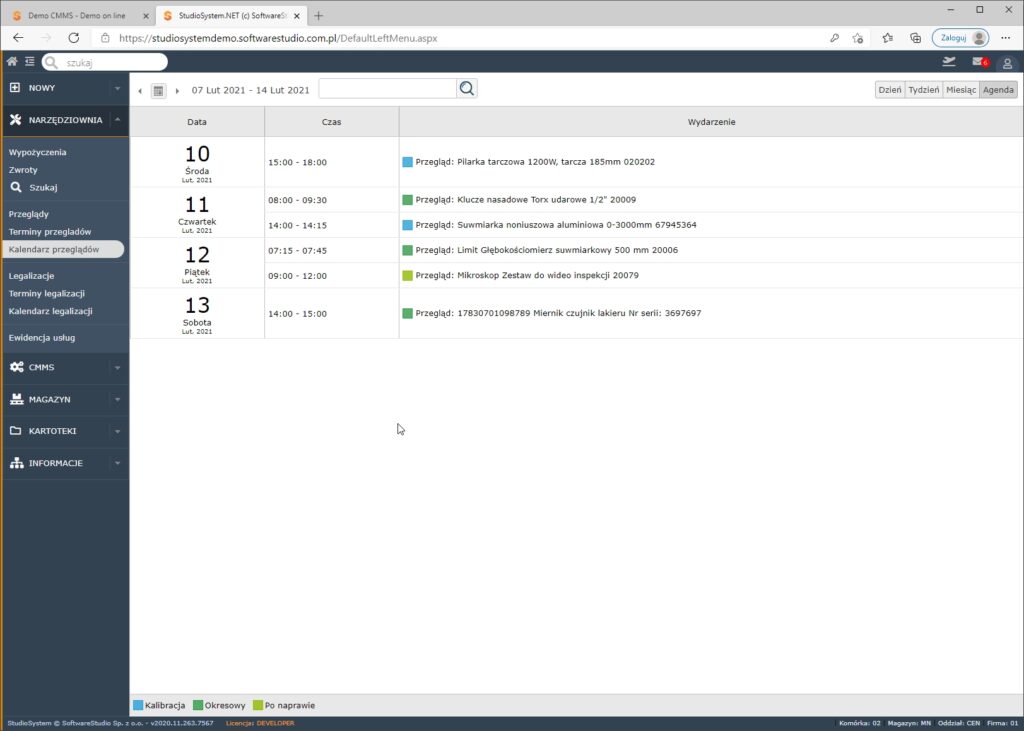
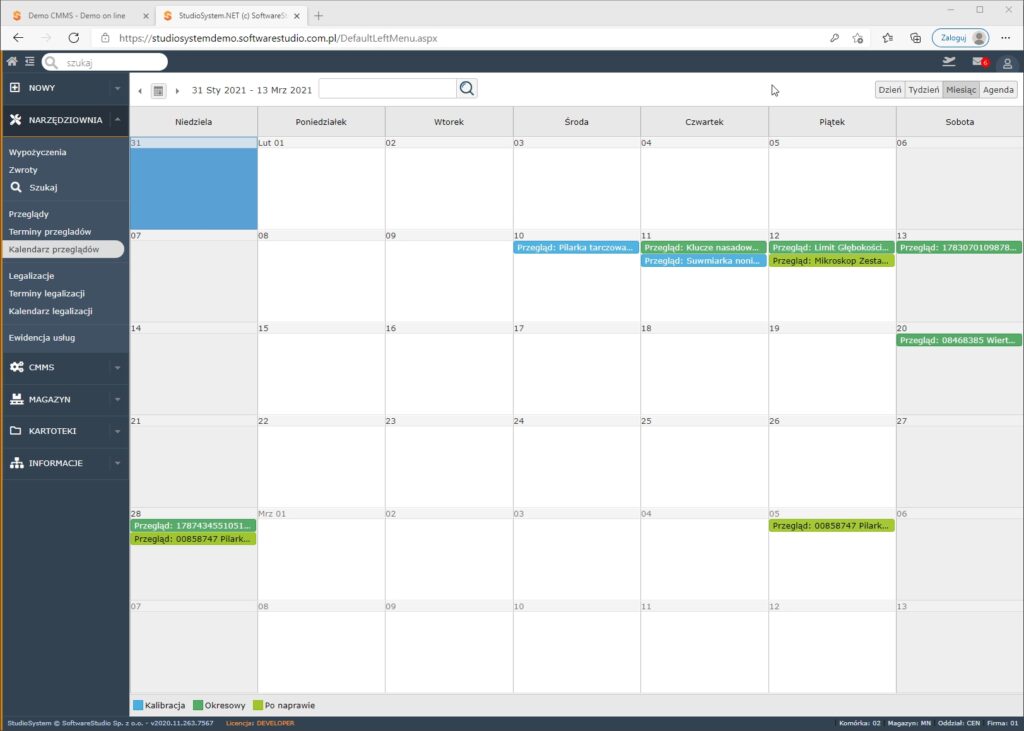
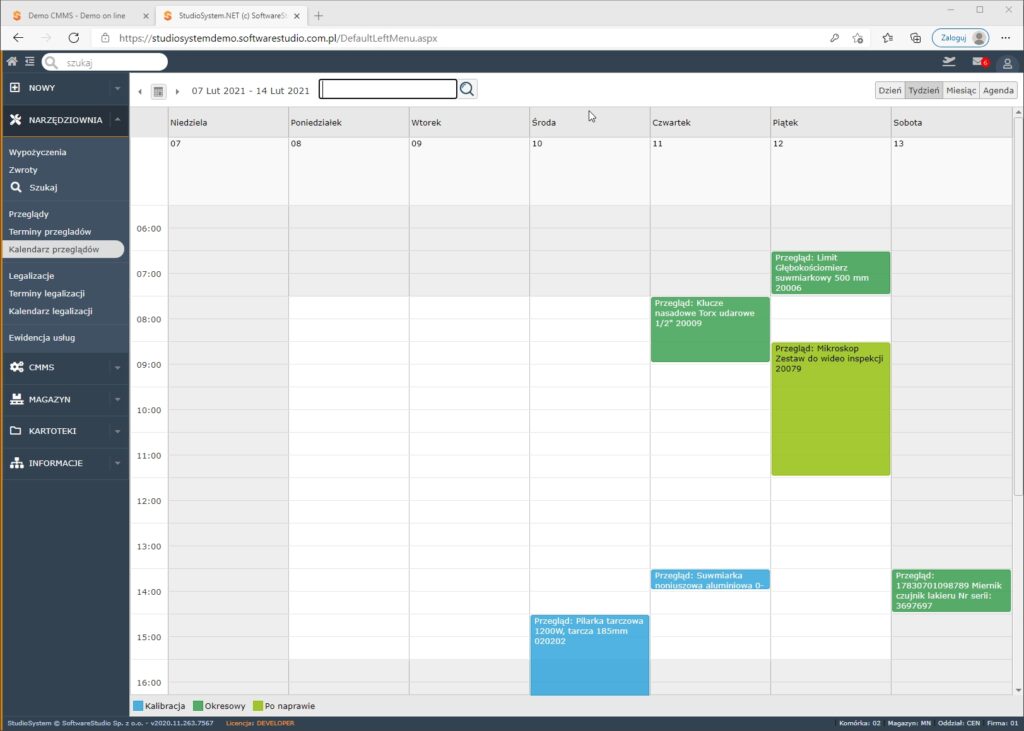
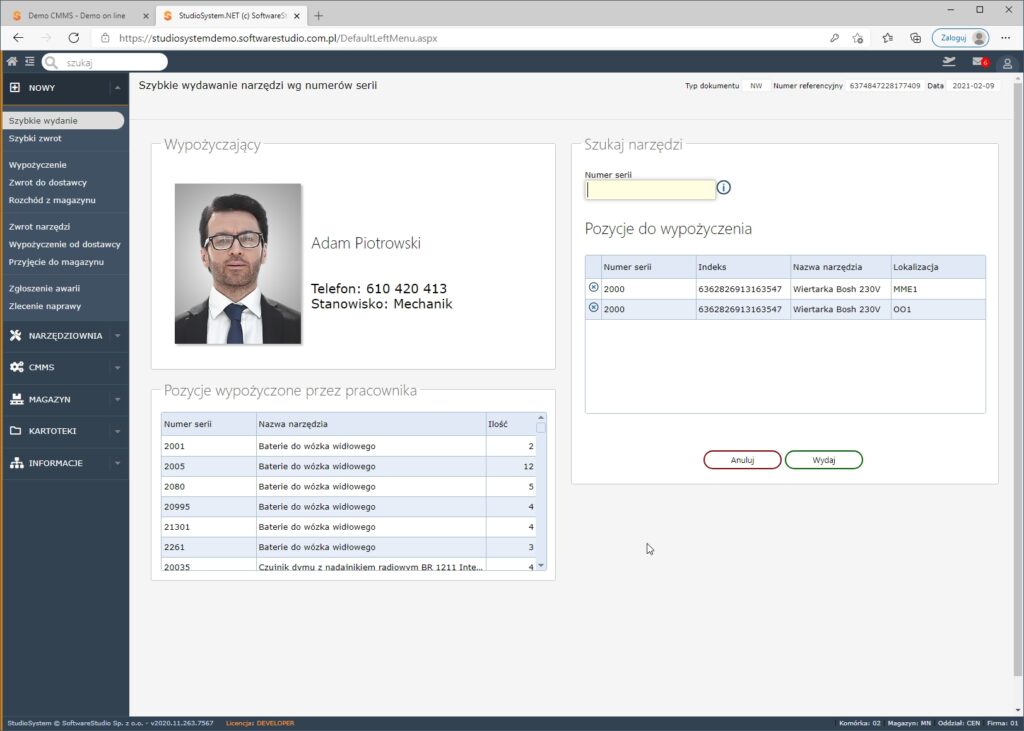
Pojęcie awarii w kontekście RCM
Rozróżnienie awarii funkcjonalnej i potencjalnej
W ramach Reliability Centered Maintenance (RCM) kluczowym pojęciem jest awaria, która może prowadzić do zakłócenia lub niemożności spełniania określonych warunków działania maszyny lub urządzenia. W kontekście RCM wyróżnia się dwa rodzaje awarii: awarię funkcjonalną i awarię potencjalną.
Awaria funkcjonalna to sytuacja, w której całe uszkodzenie lub jego zespół lub część nie jest w stanie wykonywać określonych funkcji zgodnie z wymaganymi warunkami lub standardami działania. Oznacza to, że uszkodzenie uniemożliwia lub utrudnia prawidłowe działanie maszyny lub urządzenia.
Z kolei awaria potencjalna odnosi się do fizycznie zidentyfikowanych oznak wskazujących na możliwość wystąpienia awarii funkcjonalnej w przyszłości. Mogą to być na przykład wczesne objawy zużycia, pogarszający się stan techniczny lub inne wskaźniki wskazujące na zbliżającą się awarię.
Monitorowanie w kontekście RCM
Procedura RCM w dużym stopniu polega na wykorzystaniu monitorowania w celu przewidywania momentu potencjalnej awarii. Monitorowanie stanu technicznego maszyny lub urządzenia pozwala na śledzenie wskaźników, które mogą wskazywać na zbliżającą się awarię. Dzięki monitorowaniu można zidentyfikować wczesne objawy uszkodzenia, co umożliwia podjęcie odpowiednich działań naprawczych przed wystąpieniem awarii funkcjonalnej.
Zastosowanie RCM w tworzeniu systemu utrzymania ruchu
RCM jest szeroko stosowane do tworzenia systemów utrzymania ruchu maszyn i urządzeń od podstaw. Procedura ta umożliwia identyfikację kluczowych funkcji urządzenia, analizę potencjalnych awarii i ich skutków, oraz wybór odpowiednich działań konserwacyjnych w celu minimalizacji ryzyka awarii i przestojów.
Wykorzystanie RCM w tworzeniu systemu utrzymania ruchu pozwala na planowanie i realizację działań konserwacyjnych w sposób przemyślany i efektywny. System utrzymania ruchu oparty na RCM uwzględnia monitorowanie stanu technicznego, przewidywanie potencjalnych awarii i podejmowanie odpowiednich działań naprawczych przed wystąpieniem awarii funkcjonalnej. Dzięki temu możliwe jest zapewnienie wysokiej niezawodności, dostępności maszyn i urządzeń oraz minimalizacja przestojów produkcyjnych.
Koszty utrzymania ruchu maszyn i urządzeń
Wysoki udział kosztów utrzymania ruchu maszyn i urządzeń w kosztach zmiennych przedsiębiorstwa zmuszają do intensywnego poszukiwania możliwości ich kontrolowania i zmniejszenia.
Rośnie nie tylko znaczenie samego utrzymania urządzeń w sprawności eksploatacyjnej, ale rosną także, absolutnie i relatywnie, koszty utrzymania tej sprawności.
Analiza sposobów podejścia do utrzymania ruchu urządzeń i maszyn, dokonywana w perspektywie czasowej, pozwala na wyróżnienie okresów:
- Okres reaktywnego utrzymania ruchu – remonty po pojawieniu się uszkodzenia, charakteryzuje się; doraźnym reagowaniem na wystąpienie uszkodzeń;
- Okres prewencyjnego utrzymania ruchu – planowe i zapobiegawcze;
- Okres prognostycznego utrzymania ruchu maszyn i urządzeń – inspekcje zapobiegawcze, samodzielne; przeglądy, monitorowanie stanu technicznego, udział Operatorów urządzeń i maszyn w utrzymaniu ruchu.
Sposób utrzymania ruchu określonych maszyn i urządzeń zależy od ich charakterystyki konstrukcyjnej i roli, jaką spełniają w procesie produkcyjnym. Urządzenia skomplikowane, kosztowne i pracujące w zautomatyzowanych liniach technologicznych powinny być utrzymywane bardzo starannie. Ich awaria powoduje, bowiem przestój całej linii.
Strategia eksploatacji
Strategię eksploatacyjną należy, więc dostosować do konkretnych urządzeń i maszyn oraz warunków ich eksploatacji. Utrzymanie ruchu jest połączone z wysiłkami przedsiębiorstwa produkcyjnego mającymi na celu wytworzenie produktu o wysokiej jakości, tak więc jakość środków produkcji (maszyn i urządzeń) decyduje w dużej mierze o jakości wyrobów gotowych, zależna jest, bowiem od jakości czynności utrzymania ruchu.
-
System Studio TCS.net wspiera utrzymanie ruchu i zarządzanie narzędziami
Odkryj, jak Studio TCS.net zmienia podejście do utrzymania ruchu i zarządzania magazynem narzędzi. Zobacz, jak ten program ułatwia planowanie przeglądów i optymalizację produkcji.
-
CMMS
Dzięki aplikacjom CMMS możliwe jest prowadzenie ewidencji technicznej, zarządzanie harmonogramami przeglądów i konserwacji maszyn oraz monitorowanie awarii i remontów. System umożliwia również kontrolę kosztów utrzymania ruchu, zarządzanie magazynem części zamiennych oraz planowanie i śledzenie prac związanych z utrzymaniem.
-
Aplikacje CMMS
Aplikacje CMMS (Computerized Maintenance Management System) to zaawansowane narzędzia informatyczne zaprojektowane w celu efektywnego zarządzania procesami utrzymania ruchu w organizacjach. Oferują funkcjonalności takie jak planowanie i harmonogramowanie prac konserwacyjnych, monitorowanie stanu technicznego urządzeń, zarządzanie zapasami części zamiennych oraz generowanie szczegółowych…
-
Magazyn CMMS
Magazyn CMMS (Computerized Maintenance Management System) to kluczowy moduł systemu, który umożliwia skuteczne zarządzanie częściami, narzędziami i materiałami potrzebnymi do utrzymania ruchu w firmie.
-
Oprogramowanie CMMS
Oprogramowanie CMMS firmy SoftwareStudio jest elastyczne i dostosowuje się do indywidualnych potrzeb przedsiębiorstwa, umożliwiając skuteczne zarządzanie utrzymaniem ruchu i konserwacją.
-
System CMMS
System CMMS.net firmy SoftwareStudio przeznaczony jest do prowadzenia gospodarki narzędziowej. Narzędziownia wyposażona w program może w łatwy i szybki sposób prowadzić magazyn. Ponadto rozlicza pracowników z wypożyczonych narzędzi. W systemie CMMS mamy moduły: awarii, remontów, napraw i przeglądów.
-
Narzędziownia
Narzędziownia to kluczowe miejsce w firmie, gdzie przechowywane, konserwowane i zarządzane są narzędzia niezbędne do wykonywania różnorodnych zadań. Efektywne zarządzanie narzędziami ma ogromne znaczenie dla sprawnego funkcjonowania procesów produkcyjnych.
-
Funkcje modułu ubrania w Studio TCS.net
Moduł „Ubrania” w Studio TCS.net zapewnia kompleksowe narzędzie do zarządzania odzieżą, od jej wprowadzenia do systemu, przez monitorowanie stanu i operacji, aż po wycofanie z użytku.
-
Klucz do efektywnego zarządzania narzędziami w przemyśle
Chcesz usprawnić procesy w swojej firmie? Szukasz rozwiązania, które połączy zarządzanie narzędziami z utrzymaniem ruchu? Studio TCS.net to wszechstronne oprogramowanie, które spełnia te wymagania. Ten system dla przemysłu optymalizuje wszystkie operacje, od wydawania narzędzi po planowanie przeglądów.
-
Aplikacja mobilna do skutecznej ewidencji sprzętu i prewencji awarii
Chcesz mieć pełną kontrolę nad swoim sprzętem i jednocześnie zapobiegać awariom? Studio TCS.net to kompleksowa aplikacja mobilna, która sprosta tym wyzwaniom. Dzięki niej zyskasz mobilny dostęp do wszystkich kluczowych informacji i usprawnisz działania prewencyjne.
-
Zwiększ efektywność utrzymania ruchu dzięki Studio TCS.net
Zarządzanie utrzymaniem ruchu i magazynem narzędzi to wyzwanie dla wielu firm. Szukasz sposobu na usprawnienie tych procesów? Studio TCS.net to program, który Ci w tym pomoże. Ten system kompleksowo wspiera zarządzanie zasobami i pracownikami w utrzymaniu ruchu.
-
Jak nowoczesne oprogramowanie CMMS usprawnia zarządzanie utrzymaniem ruchu w Twojej firmie
Odkryj Studio TCS.net i zobacz, jak rewolucjonizuje zarządzanie utrzymaniem ruchu. Poznaj jego kluczowe funkcje i dowiedz się, jak optymalizuje procesy konserwacji w przemyśle.
-
Program CMMS
Oprogramowanie CMMS jest ważnym narzędziem do zarządzania i planowania utrzymania ruchu zakładów przemysłowych. Zakłady przemysłowe posiadają wiele złożonych i powiązanych ze sobą systemów, które muszą być utrzymywane w niezawodny i bezpieczny sposób. Oprogramowanie CMMS pomaga kierownikom zakładów śledzić i planować…
-
Użytkownicy programu magazyn narzędzi
Oprogramowanie CMMS zazwyczaj zawiera bazę danych sprzętu i części, system zleceń pracy, system konserwacji zapobiegawczej i system śledzenia czasu. Baza danych sprzętu i części umożliwia kierownikom zakładów śledzenie lokalizacji i stanu wszystkich urządzeń w zakładzie. System zleceń pracy umożliwia kierownikom…
Aplikacje CMMS
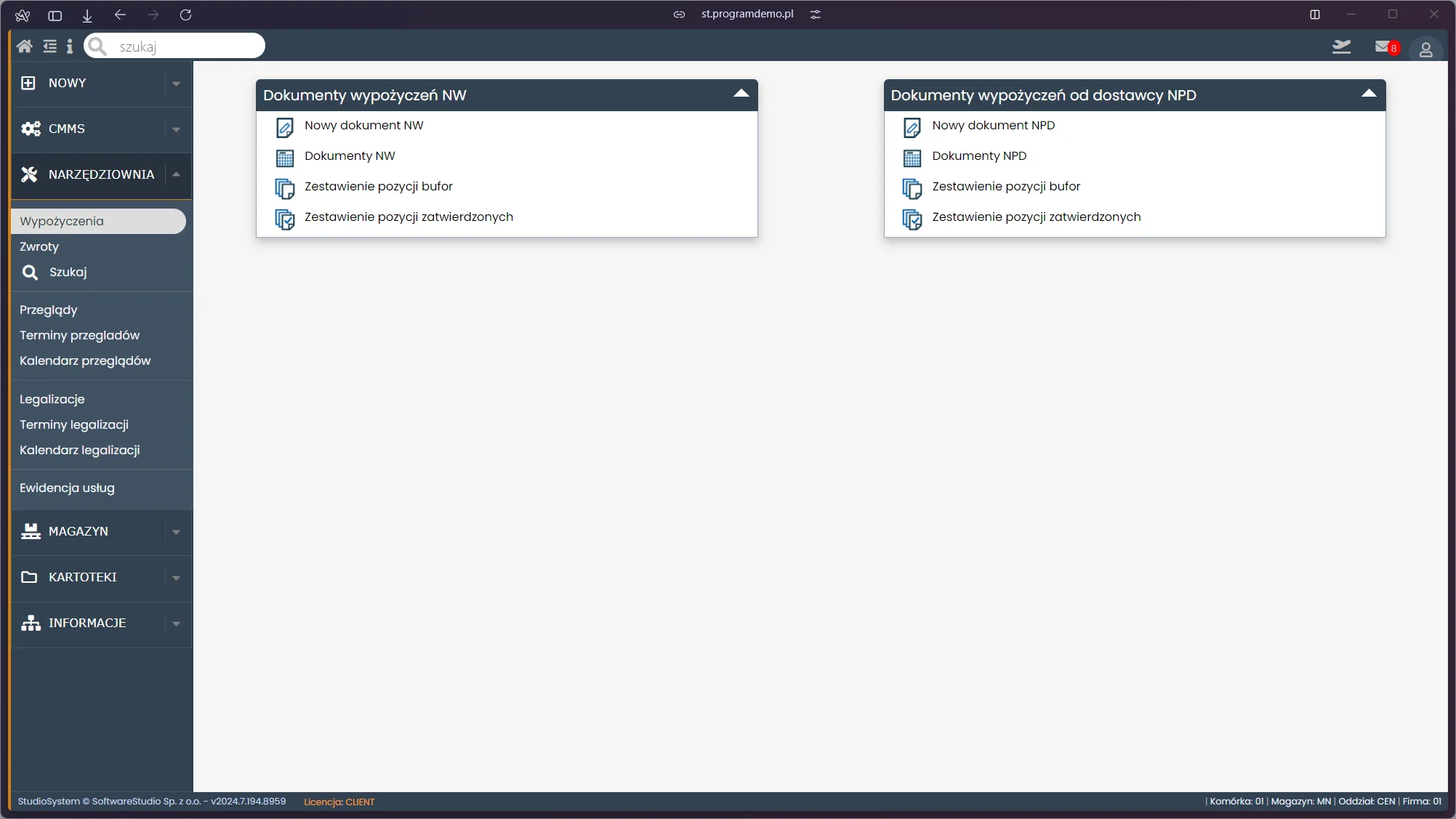
Administrator programu CMMS
Administrator w programie CMMS zarządza utrzymaniem ruchu, monitoruje stan techniczny maszyn oraz planuje przeglądy i naprawy. Ta rola minimalizuje ryzyko awarii, zwiększa wydajność urządzeń i poprawia efektywność pracy. Administrator dba o terminowe wykonanie prac konserwacyjnych, co zapobiega nieplanowanym przestojom i zapewnia ciągłość produkcji. Dodatkowo monitoruje stan maszyn, aby szybko wykrywać problemy, unikając poważnych uszkodzeń iSystem Utrzymania Ruchu

System utrzymania ruchu
Wybierz nasz system CMMS, aby skutecznie zarządzać utrzymaniem ruchu w Twojej firmie. Precyzyjnie planujesz przeglądy i konserwacje, co minimalizuje ryzyko nieoczekiwanych awarii maszyn. Zyskujesz pełną kontrolę nad parkiem maszynowym, optymalizujesz koszty i znacząco podnosisz efektywność operacyjną całego zakładu.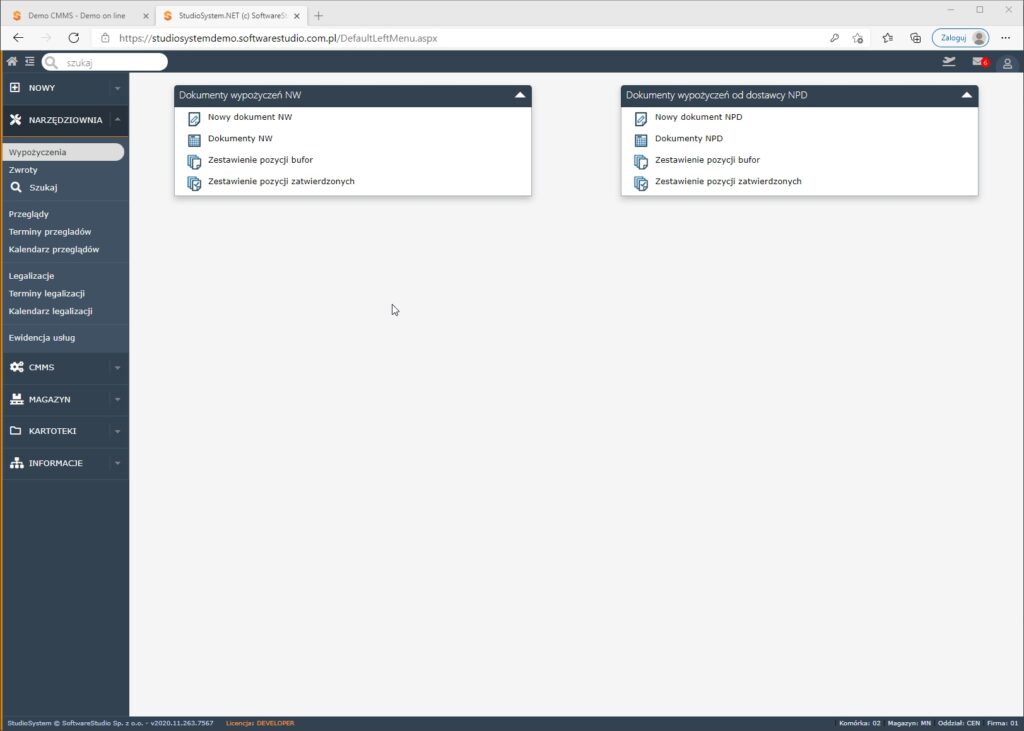
Utrzymanie ruchu maszyn
Konserwacja zakładów przemysłowych ma kluczowe znaczenie dla zapewnienia optymalnego funkcjonowania i wydajności. Jednak śledzenie zadań konserwacyjnych i zarządzanie nimi może stanowić wyzwanie, szczególnie w przypadku dużych obiektów z wieloma systemami. Tu właśnie wkraczają komputerowe systemy zarządzania utrzymaniem ruchu (CMMS).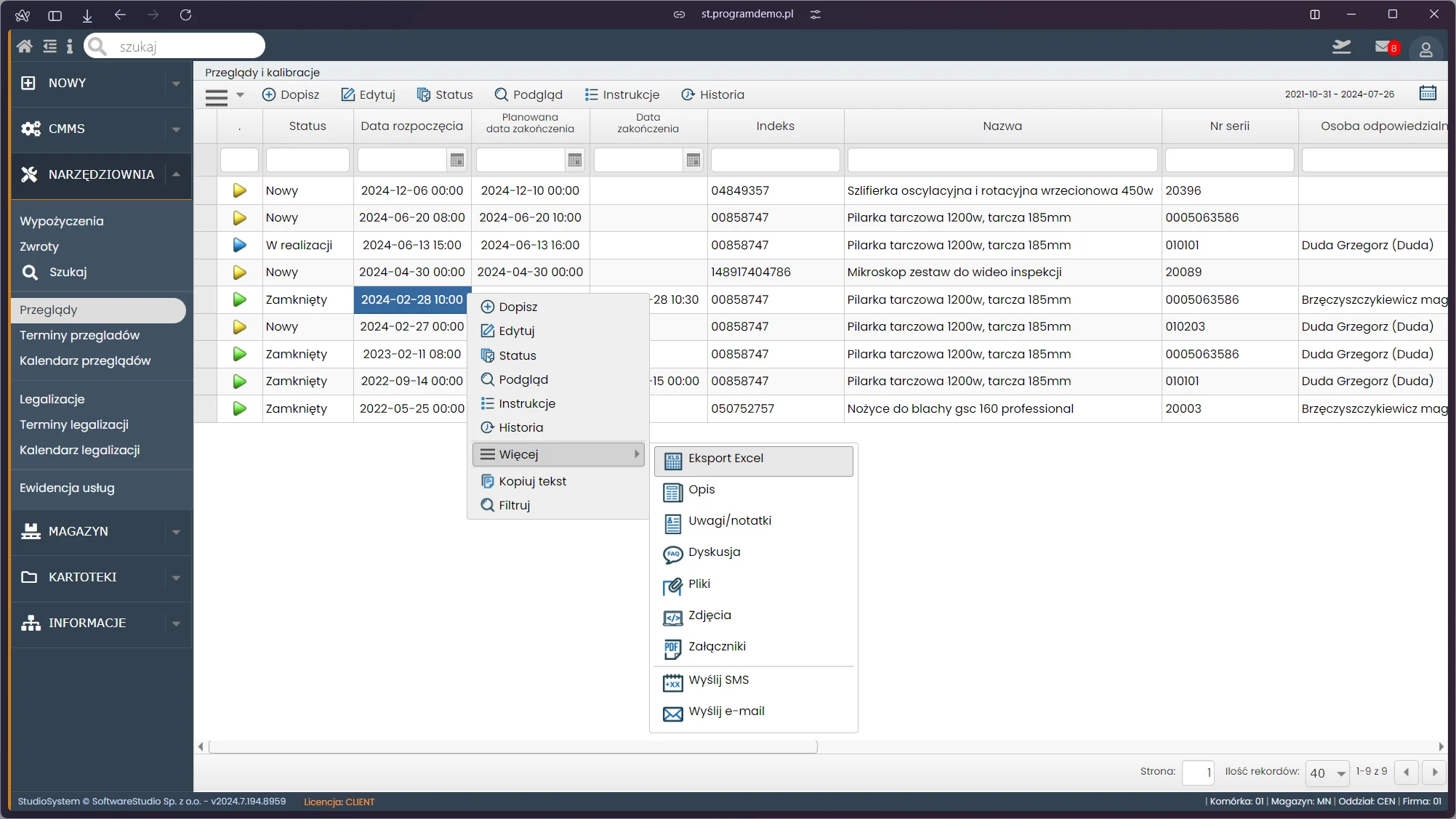